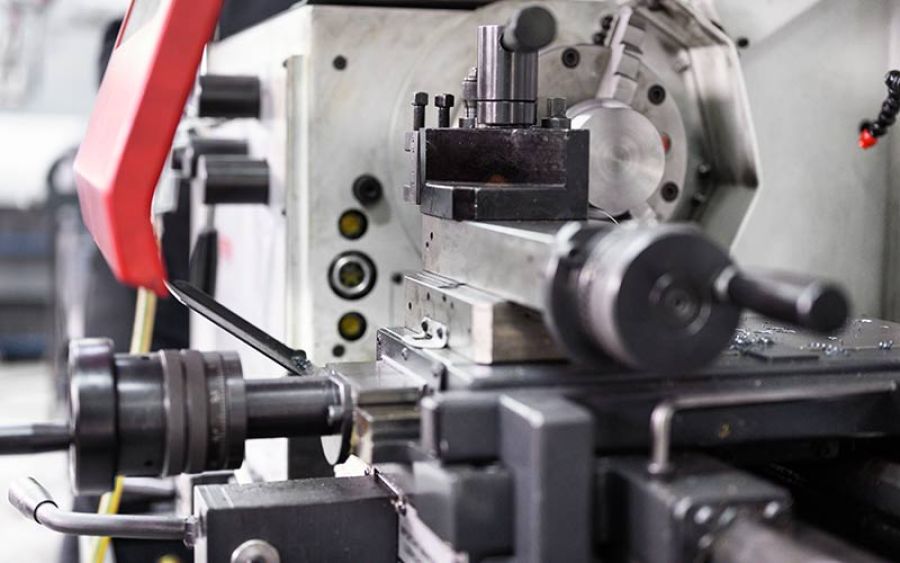
Impeller machining case of five-axis linkage machining
Impeller blades are the core components of aero engines, steam turbines and other devices. Impeller refers not only to the wheel disc equipped with moving vanes, but also to the general term of the wheel disc and the rotating blades installed on it. The turbine blades in the aero engine are in the parts with the highest temperature, the most complex stress and the harshest environment, and are called the first critical parts.
Due to its complex curved surface structure and almost harsh application environment, impeller blades are the most typical difficult-to-machine structural parts. Impeller blade processing, known as the "peak arena of five-axis machining", can be seen in its typical role in machining technology, its advanced processing program, by the attention and pursuit of domestic and foreign technology experts.
In view of the processing problems of aerospace impeller blades, we recommend several processing solutions for you today.
First, the choice of tools
1. In order to improve the processing timeliness, large fast feed and large depth of cut tools should be selected as much as possible to rough machining the blades, which can improve the processing efficiency; Hips recommends the use of SD fast feed series, XC large depth of cut series, UFO flying saucer self-rotating series;
The nano-scale tungsten carbide particles used in the above-mentioned tools are finer than the tungsten carbide particles that constitute the conventional cemented carbide tools, and can achieve the requirements of fast feed and large depth of cut; In addition, the surface of the tool is specially treated and then coated with a layer of PVST coating, which not only improves the overall performance of the tool, but also ensures the sharpness of the cutting edge, which is excellent when machining superalloy materials.
Second, the choice of tool handle
The structure of the tool holder is divided into two types: integral type and modular type.
- Modular tool holders: In order to adapt to the change of parts and machines, the user must stock various specifications of tool holders, so the utilization rate of tool holders is low. The modular tooling system is a state-of-the-art tooling system in which each toolholder can be assembled from a variety of serialized modules. Hips recommends the Dream 5-axis linkage series, which adopts different assembly solutions for different machined parts and machine tools, which can obtain high stability and flexible combination, so as to improve the machining efficiency and cutting quality of the tool holder.
- Integral tool holders: Generally, people like collet chucks and power tool holders, but in the case of large chip force, there may be loosening of the locking method and cause tool drop or over-cutting. Therefore, Hips recommends the use of heat shrinkable series to solve the phenomenon of knife drop and gouge in the application of tools for our customers; The heat shrinkable tool holder is the working principle of thermal expansion and cold contraction, the tool is firmly clamped, and no mechanical clamping parts are involved between the tool and the tool holder, giving uniform pressure to the tool clamping surface, so as to produce a high radial clamping force. As a result, the balancing, slew accuracy, and clamping strength, which are extremely important in high-speed finishing, can be solved.